Laser Beam Shaping
The laser is a universal tool in materials processing. Focusing a high-power laser to a single spot allows various applications like welding and laser-based additive manufacturing. Heating and consequent melting of the material mainly drives these processes in which the laser beam acts as a heat source. For the processing result, resolidification is critical as defects like cracks can occur but also spatter might be produced during laser interaction due to overheating and turbulences in the melt pool. An important factor for these defects is the heat distribution in the work piece.
State-of-the-art lasers produce a focus that resembles either a bell (Gaussian) curve or a rectangular (top-hat) shape and therefore the resulting heat profile is predefined. Beam-shaping is a technique for influencing the shape of the focus and therefore forming the heat profile in a desired manner. This offers the possibility to mitigate defects and increase the processing window as well as the production efficiency.
To shape laser beams, so-called diffractive optical elements can be used, which are glass slides with a surface relief of a few micrometers. By introducing a phase delay, they influence the propagation of light. The Institute of Photonic Technologies (LPT) works on predicting optimized beam shapes for specific applications, calculating the appropriate relief, and showing advantages in materials processing. As an example, this technique was successfully used at LPT for welding a crack-prone aluminum-copper alloy, which resulted in a weld seam quality close to a polished surface and an enlarged processing window.
Beam-shaping also offers the possibility of processing large areas at once, for example engraving product information without having to move the laser beam. For designing elements for large-area processing, the main challenge is the presence of speckle, which are artefacts due to undesired interference of light. LPT develops setups and algorithms to reduce the influence of speckle during processing. For testing new developments, low average power pulsed lasers are employed which allow using liquid crystal spatial light modulators instead of static diffractive optical elements. These modulators work similar to LCD screens and allow quickly displaying different structures without having to manufacture a new glass element each time. By using two sequential modulators, researchers from LPT showed speckle-free large-area beam-shaping.
Ongoing research includes the direct manufacturing of beam-shaping elements in bulk glass, which would offer more degrees of freedom compared to a relief. Beyond additive manufacturing, beam shaping also plays an increasing role in other directions of research, for example as a tool in optical metrology.
By Clemens Roider
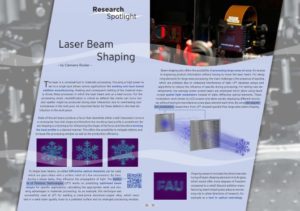